From the leather tip, to the rubber bumper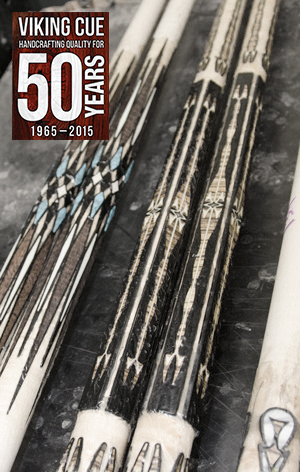
A Viking cue is constructed with the best components, experience, and care in the billiard industry. We manufacture 99% of the parts we use on our cues and guarantee that our product is 100% American made. All Viking cues come standard with an Everest tip by Tiger. The tip is bonded to our specially designed ferrule that is the best in the industry. Our ferrule material is extremely durable and will not stain, crack, or burn, for as long as you own your cue, we guarantee it. The design of the ferrule and the tenon, on which it is attached to the solid maple shaft, is designed to provide a solid hit on the cue ball with minimal deflection. This translates simply to more shots made and less miscues.
Quick-Release Joint
We have designed our joint pin and female with two things in mind; first and most importantly is strength, secondly is convenience. Our joint components are designed and manufactured in our factory from high-grade stainless steel and brass. It takes approximately 5 turns to secure the shaft to the butt, then your cue is ready for action. The joint of each cue is installed by a CNC controlled machine to assure a perfectly concentric union. Every pool cue joint features wood to wood construction for the best possible feel. Different joint collar combinations are available to modify the softness/hardness of the cues hit.
Indestructible
All Viking Cues feature the finest ferrule the billiards industry has ever known. Formulated from a proprietary material, the Viking SUPER ferrules are virtually indestructible! We put our ferrules through the industry’s toughest impact tests; it’s more like a torture test. With 250,000 in play and no cracked ferrules, you know we’ve done our homework. No other ferrule in the business can say that.
Weight-Bolt System
Our unique weight system is comprised of precisely weighted "weight-bolts" and a CNC bored and threaded chamber inside the cue's butt unit. This allows the cue to be weighted and balanced accurately to suite your preference. The pool cue's weight can be increased or decreased simply by using a 1/4" hex wrench to add or remove weight-bolts.
Shafts
Through new technology, advanced design, careful craftsmanship, and world‑class performance, our eXactShot®, ViKORE® shafts and VPRO® shafts won’t just help you reach your full potential, but perhaps to exceed it. It all starts here. Every shaft we make goes through a multi-stage cutting and curing process. We consider our shaft curing process the most effective and superior in the industry. Each piece of wood is hand graded by a well experienced craftsman a minimum of 3 times throughout the shaft turning process. Every shaft is cured for a minimum of 2 years in our temperature and humidity controlled warehouse. The main characteristics we look for are: wood grain straightness, wood density, and the color of the wood.
Finger Joint Construction
The butt end of each Viking pool cue is built with hand-selected wood, and then finger-jointed together to guarantee a straight and solid cue. In addition to strength and straightness, finger-joint construction can aid in balancing the weight distribution of the cue from the joint to the butt.
finishing
Our finishing process is the most time consuming, and rewarding step of making a Viking cue. The first step, if necessary, is staining the wood. We lock in the rich color with a sealing coat and then it's off to the fully automatic spray booth. Our custom spray booth applies our high-tech finish to the cue and then passes it in front of a special ultraviolet light to harden and cure the finish. The cue then goes through a multi-stage buffing and polishing process to make it shine like glass.
About the BUTT
The typical butt assembly of our cues consists of three pieces of wood finger-jointed together, to improve the strength, balance, and straightness of the finished butt. The butt is then "rough-cut" to a specific diameter, uniformly stacked, then stored in our environmentally controlled warehouse. The wood is allowed to cure for a minimum of 2 months before it gets worked again. Once the curing is complete, the cue is machined again, this time it's the inlays, rings, joint-collars, and butt-caps that are installed. The butt's diameter is turned down one more time to the finished dimensions. We let the butt sit and cure one more time before moving on to the finishing process.
WRAPPING IT UP
Wrapping a cue takes a skilled hand and lot of practice, but the outcome is beautiful. Irish Linen is generally used for the wrap area of the cue, this not only looks very nice, but it also gives you a solid spot to grip your cue. We also offer no-wrap, leather, and finish-over-wrap as an alternative. Last but not least, weights are installed inside the butt of the cue to achieve the desired weight. We thoroughly checked over the entire cue one last time, then seal it in a bag. Now it's ready to be shipped off to some lucky pool player somewhere in the world.